
Printing Explained
Bringing all the pieces together
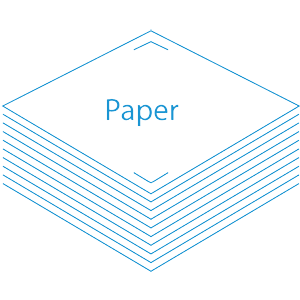
Paper Types
Coated Paper
Coated paper has been coated with a surface sealant, typically clay, to impart certain qualities to the paper, including weight, surface gloss, smoothness or reduced ink absorbency. The coating on the paper reduces dot gain by not allowing the ink to absorb into the paper. This allows for cleaner crisper printing, especially in photos, blends and fine details. Coated papers come in numerous options: gloss, matte, dull and satin finish.
Gloss — gloss coated paper has a high sheen. Gloss papers have less bulk and opacity and are typically less expensive than dull & matte paper of equal thickness. Gloss coatings reduce ink absorption, which give the sheet an excellent color definition.
Satin — a satin coating is a less shiny coated finish. It has a lower gloss level than gloss finish, yet a higher gloss level than matte finish. Colors are sharp and vivid.
Matte — a matte coated paper is a non-glossy, flat looking paper with very little sheen. Matte papers are more opaque, contain greater bulk, and are higher in cost. The coating still keeps much of the ink from being absorbed by the paper, which produces excellent, vibrant color.
Dull — a dull finish coated paper is a smooth surface paper that is low in gloss. Dull coated paper can fall between matte and glossy paper depending on the manufacturer.
Uncoated Paper
Uncoated paper stock is paper that has not been coated with a surface sealant. Inks dry by absorbing into the paper. This paper type can dull the colors that are printed. Uncoated papers comprise a vast number of paper types and are available in a variety of surfaces, both smooth and textured. Some of the common types are wove or smooth, laid and linen.
Wove or Smooth — this has a very smooth surface.
Laid — laid paper is created with textured lines on its surface. This finish is used mostly for business stationery elements, like letterhead, envelopes and business cards.
Linen — similar to a laid finish, this paper has textured lines on the surface of the sheet, but they are finer and more regular than those that appear on a laid finish stock. This paper is also used frequently for business stationery.
See detailed for comparison chart Uncoated Commercial Printing Papers.
Coated One Side and Coated Two Slides
This paper is commonly referred to as C1S (coated one side) or C2S (coated two sides). In a C1S paper the coating has been applied to only one side of the paper. C2S the coating is on both sides. Typically the coated side is glossy. You will find this type of paper used primarily on postcards. It gives a glossy feel to the front of the card while using the back uncoated side for addressing.
Weight
The weight of a paper refers to its thickness and is typically measured in pounds (such as 20#) and points (such as 10 PT). The higher the number, the thicker the paper for that “type” of paper. Paper weights in commercial printing can be very confusing. For example, a sheet of 20# bond (probably what you use on your inkjet printer) is about the same thickness as a sheet of 50# offset.
There are three general paper categories used to describe the basis weight of a paper: writing, text and cover.
Writing — a letterhead-weight stock, typically 24# or 28# writing, and often has a watermark.
Text — is thicker than a writing paper, but not as thick as a cover paper (card stock). Text-weight paper is usually a 70#, 80# or 100# text.
Cover — Cover stocks are heavy in weight, rigid and not easily folded. Common weights for cover stocks include: 65#, 80#, 100#, 120#, and 12pt.
Opacity
A paper’s opacity is determined by its weight, ingredients and absorbency. A paper’s opacity determines how much printing will show through on the reverse side of a sheet. Opacity is expressed in terms of its percentage of reflection. Complete opacity is 100% and complete transparency is 0%.
Brightness
The brightness of a sheet of paper measures the percentage of a wavelength of blue light it reflects. The brightness of a piece of paper is typically expressed on a scale of 1 to 100 with 100 being the brightest. The brightness of a paper affects readability, the preception of ink color and contrast betwwen light and dark hues.
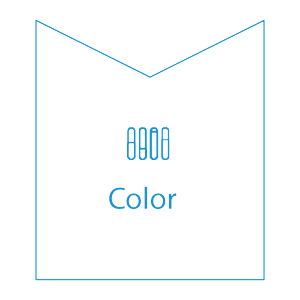
Color
Spot vs. Process Color
There are two main printing processes: 4 color process (CMYK) printing and spot color printing printing.
Spot Color
Spot color printing creates brighter, more vibrant results, but with a smaller color range. When printing in single (spot) colors, a single color ink (normally with a Pantone reference number) is applied to the printing press roller. If there is just one color to be printed, there will be a single plate, and a single run of the press. If there are two colors, there will be two plates and two runs, and so on. The colors are layered onto the paper one by one.
Spot color printing would be typically used for jobs which require no full color imagery, such as for business cards and other stationery, or in monotone (or duotone etc) literature such as black and white newspaper print.
Process Color
4 color process printing involves the use of four plates: Cyan, Magenta, Yellow and Keyline (Black). The CMYK artwork (which you will have supplied) is separated into these four colors – one plate per color. The four CMYK inks are applied one by one to four different rollers and the paper or card (‘stock’) is then fed through the printing press. The colors are applied to the stock one by one, and out comes the full color (4 color process) result.
Here is an example of 4 color process printing and three examples of spot color printing. There is a lot of versatility in designing for a spot color print run—experiment and see what results you can achieve!
Process color printing, also known at four-color process printing, is a method that reproduces finished full-color artwork and photographs. The three primary colors used are cyan (process blue), magenta (process red), and yellow. These inks are translucent and are used to simulate different colors, for example, green can be created using cyan and yellow. The “K” in CMYK is black. Black ink is used to create fine detail and strong shadows.
Artwork and photos are reproduced when the colors in the artwork are separated, then halftoned (converted to dots). Process colors are reproduced by overlapping and printing halftones to simulate a large number of colors.
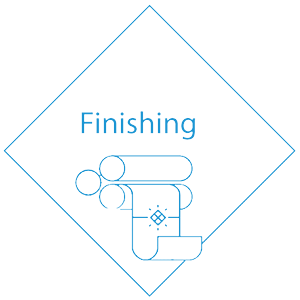
Finishing
In the print business, Finishing refers to operations that are performed after the ink has beenapplied to the paper. Some finishing operations can occur before the printing comes off the press, but many finishing operations are performed after the printing comes off the press.
Here is a simple breakdown of some of the services that fall into finishing:
Collating
The gathering and arranging of individual sheets or other printed components into a predetermined sequence. Collating creates consistent, logical sets from multiple parts.
Cutting and Trimming
Using a sharp blade or shear to reduce a printed piece down to its desired size. Common examples include removing excess paper along crop marks, separating pieces that have been printed as multiple images per sheet, or trimming the open edges of a book to create evenly aligned pages.
Scoring
The process of making a crease in paper so it will fold easier. Helps improve the appearance of the fold because it provides a consistent guideline. Used mostly on heavyweight papers and cardstock.
Folding
A procedure that bends over a printed piece so that if lays flat upon itself. Folding serves many functions, one of which is to reduce the physical size of a printed piece. This allows the piece to fits into something else – like an envelope, packaging, or display rack. A smaller size can also make certain printed items easier to handle and/or distribute. Folding is also commonly used as a design technique to create separate panels from a single sheet, such as for a brochure or invitation. There are numerous folding styles available, including the popular c-fold, z-fold, gatefold, and mini fold.
Laminating
The process of bonding a clear plastic film onto printed matter to protect it against stains, smudges, moisture, wrinkles, and tears. Greatly improves durability. Also enhances the vibrancy of the ink colours. Lamination is a popular choice for printed items that must endure heavy use, such as educational materials, flip charts, book covers, restaurant and bar menus, and consumer displays.
Die-Cutting
Using a thin sharp blade that has been pre-formed into a specific pattern or outline to cut paper, cardstock, labelstock, or other substrates into varius shapes.
Perforating
A procedure that creates a series of very fine holes in paper or cardstock, usually along a straight line, to allow a portion of the printed piece to be easily detached by hand. Used for a variety of purposes, such as coupons, ID cards, response cards, and remittance slips.
Sequential Numbering
Involves the printing of ascending or descending identification numbers so that each printed unit receives its own unique number. This unique number can appear in one position, or in multiple positions, on each document. In addition to providing a method for easy reference, sequential numbers provide a high degree of accounting control. Frequently used on contracts, invoices, purchase orders, quote forms, checks, raffle tickets, contest entries, or virtually any printed item that needs unique identification.
UV-Coating
A tough clear-coat applied over printed materials to improve resilience and appearance. This coating is applied in liquid form, then exposed to Ultra-Violet light which bonds and dries it instantly.
Aqueous Coating
An economical water-based clear-coat applied to printed pieces to help protect the ink and paper against minor scuffs and abrasions.
Drilling
Refers to the process of creating round holes in paper using a rotating bit, such as the hole patterns needed for sheets and dividers placed into ringed binders.
Embossing / Debossing
Refers to the method of pressing an image into paper or cardstock to create a three dimensional design. Embossing results in a raised surface; debossing results in a depressed surface.
Foil Stamping
A specialized process that uses heat and pressure to apply a metallic foil design to a printed piece. The foil is usually a gold, silver, or copper tone, though a variety of colours are available. Foil stamping adds elegance and distinction and can be combined with the embossing technique to create a metallic design in relief.
Padding
Applying a flexible adhesive along one edge of a stack of same-sized sheets. The adhesive secures the sheets as a unit, but allows the topmost sheet to be easily removed as needed. In most cases, padded sheets incorporate a chipboard backer for rigidity. Common examples include notepads, memo pads, and order pads.
Shrink Wrapping
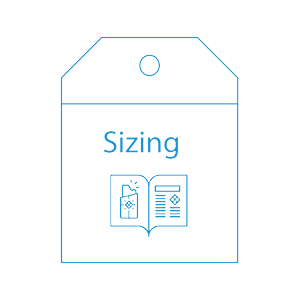
Sizing
We express paper dimensions in inches because we work with both non-standard and standard size books. 5.5 x 8, 7 x 10, 8.5 x 11 are all common book printing sizes, but since we can produce books of any size, it’s easier to stick with inches rather than only working with standard paper sizes. However, since many customers are already familiar with those standard sizes, we hope this chart will serve as a reference point for those deciding the best size for their book.
Since it’s occasionally not clear whether horizontal dimension or vertical dimension comes first when expressing paper size, note that all examples here (as well as all the dimensions you can choose on our quote page) are listed as horizontal width x vertical height. In a related note, you’ve probably also heard of portrait and landscape page orientation. Portrait means the layout has a greater height than width; landscape is wider than it is tall.
So here’s a group of charts of common paper sizes, and below that you’ll find a brief history of how some of these sizes came to be today’s standards (which some of us paper nerds find interesting).
Common U.S. Press Sheet Sizes chart
Envelope sizing chart
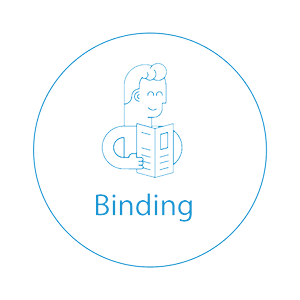
Binding
Here are descriptions of several ways you can attach loose sheets of paper or complete signatures (printed press sheets folded multiple times to yield complete 4-, 8-, 16-, or 32-page portions of a book). Bindery methods vary according to cost, durability, and appearance.
Case Binding
Also called edition binding, this method results in what is commonly called a hardcover book. It is the most expensive option yet also the most durable. Stacked signatures are gathered and sewn together for strength. This book block is trimmed on three sides and then glued into a spine, front cover, and back cover (a single unit) made of binders board covered with paper or cloth. The first and last sheets (end-sheets) are then pasted to the board. To reduce the cost of this binding method, you can set perfect-bound book blocks into cases rather than first sewing the signatures together and then gluing them into the covers.
Perfect Binding
Like case-bound books, perfect-bound books are also made up of stacked signatures. These are gathered into a book and the edges of the spine are ground off (or notched). When this book block is glued into a paper cover, the glue that attaches the signatures to the spine can flow into the notches or ground-0ff areas. The increased surface area for the glue allows for more permanent adhesion. The covers and book blocks are then trimmed flush. Unlike case binding, perfect binding involves only gluing the spine to the cover. Without reinforced endsheets or a binders board cover material, perfect-bound books are less durable than case bound books but are significantly cheaper. Sewing the signatures and/or notching the spine rather than grinding it improves durability.
Lay-Flat Binding
Perfect-bound books do not lie flat when opened because the spines are fully glued to the cover.By using a flexible glue on only the edges of the spine, perfect-bound techincal manuals or cookbooks, and the like, can be made to lie flat on a table. This method is more expensive than perfect binding and requires more time for the glue to cure.
Saddle-Stitching
Signatures are nested (set one into the other rather than stacked as in the previous methods) and then stitched through the fold with staples made of thin wire. These books can lie flat. However, saddle-stitching only works for shorter books of up to 80 pages or so. These books also have no spine on which to print a title.
Side-Stitching
Side stitched books are essentially loose sheets of paper stapled together. A paper cover can be wrapped around the entire stack and glued to form a printable spine. However, side-stitched books (National Geographic Magazine is an example) do not lie flat.
GBC Binding
Also called plastic comb binding, this method is good for technical manuals that have a lot of pages and must lie flat. The stack of pages comprising the book is punched with a series of holes along the binding edge through which a plastic comb is inserted. This comb, which curls into a cylinder along the length of the book can provide a screen-printable spine. It can also accommodate numerous pages, and pages can be added or removed as needed.
Wire-O and Spiral Binding
Both of these mechanical bindings hold far fewer pages than comb binding. Wire-O is a series of parallel wire loops attached along a wire, while spiral binding is a metal or plastic continuous loop passing through the punched holes in a spiral from the top to the bottom of the book. Neither binding method will accept as many pages as GBC. Also neither provides a printable spine or allows for pages to be added or removed. However, both binding methods allow the product to lie flat.
Plastic Coil Binding
This is just like spiral binding. However, since wire can be crushed, plastic is a resilient alternative. Also, plastic coil bindings come in multiple colors.
Tape Binding, Post Binding, and Velo Binding
These are often used for presentations. In the first case, the covers and book pages are taped together over the binding edge. In post binding, screws are used in much the same way as side stitching (but the books can be disassembled and pages can be added or removed). In velo binding, a thin, flat piece of plastic runs the length of the bind edge on the front and back of the book, and thin plastic pegs attach the two through the pages of the book.
Ring-Binders
This is exactly what the name implies: the binders we used in school. The vinyl covers can be silk screened or paper inserts can be printed and then inserted behind the clear covering of some ring-binders.
Mechanical bindings (GBC, Wire-O, spiral, plastic coil, tape, velo, post, and ring) are more expensive per unit than perfect binding or saddle-stitching, and unlike most offset printing operations, their unit cost does not decrease with increased volume. They also require ample margins since they take up a lot of room at the bind edge. On the positive side, they can allow for the inclusion of many inserts of various types and sizes within the text. Because of their cost, mechanical bindings are usually best suited to short runs.
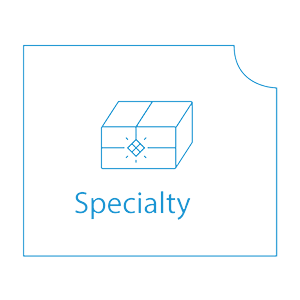
Specialty
Here are descriptions of several ways you can attach loose sheets of paper or complete signatures (printed press sheets folded multiple times to yield complete 4-, 8-, 16-, or 32-page portions of a book). Bindery methods vary according to cost, durability, and appearance.
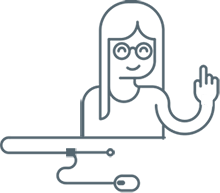
Speak to a printing expert
Call 1-888-977-7839
Email rostreicher@ptexgroup.com